Introduction to Milling bits
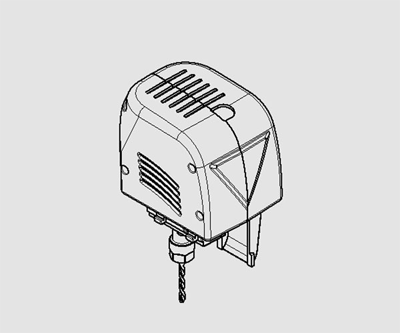
The FABtotum Milling Head V2 and Hybrid Head both natively support milling bits with a shank diameter in the range of 3.0 to 3.5mm (0.12 inches or 1/8“)
The above ER8 Collet can be swapped with another compatible one in the ER8 family.
Additional ER8 Collets allow to mount endbits with shank diameter from 1 to 5mm.
Endbits (or Milling cutters) comes in different shapes and sizes, each one for a specific purpose.
Engraving is usually done with fine, point-shaped endbits at higher speeds. Cutting and Roughing of the stock piece are usually done with flat roughing end mills while finishing in 3D milling is done with fine ball nose cutters.
Endbits remove the material by “biting” it away with their flutes while spinning. Each endbit can have a different amount of cutting flutes depending on the diameter and the purpose. The Number of flutes refers to the number of cutting edges that are cut into the body of the tool. More flutes increases the strength of the tool, but reduces space for chip flow. You can cut fast with a single flute tool, but the finish of a three or four flute cutter will be smoother.
Since the number of flutes increases the friction on the tool, which causes the tool to heat up. Some materials, like acrylic or PMMA, require the use of tools with fewer flutes in order to reduce the heat and avoid melting the material. Ideally the tool should never create waste material (chips) that are hotter than room temperature, but that can change very dramatically from material to material.
The speed at which a bit is spun is described in RPM (revolutions per minute).
Every bit has an ideal range of speed or RPMs it needs to operate within.
The ability to change the routers’ RPM is essential to good bit life and a good finish.
Vibrations should also be kept at bay. The fewer the flutes, the larger the vibration on the tool, as the load is always
localized instead of being distributed among more flutes.
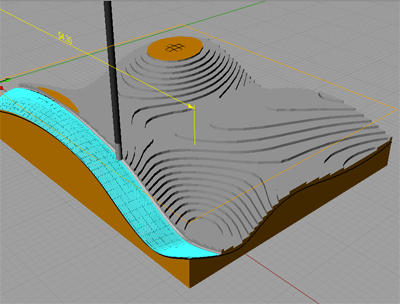
If the tool is going too fast it will heat very quickly, increasing wear and may break. The added stress may ruin the motor spindle.
But how fast is too fast? The concept is better described with the concept of Chip Load.
Chip Load is commonly referred as the amount of material each tool can remove from the stock. Chip Load is dependent upon the feed rate, rotational speed and number of flutes. Each type of material will have a range of optimal chip loads.
If the speed at which the tool is proceeding in the material is too much considering the speed at which the tool is removing material then the chip load is too high.
If the chip load is too high noise and vibrations will increase and this usually leads to damages to the endbit.
This leads to the concept of cutting depth. Since you can determine the cutting depth at which the tool operates, a deeper cut will increase the chip load, while a more shallow cut will reduce the chip load. But a shallow cut will stress the tip of the tool more, reducing its capability to plunge effectively in to the material in its lifecycle.
A finishing pass does require more passes to get a smoother surface. flat endmills are usually used only in roughing operations while ball nose cutters are used for finishing contours so you get less of a jagged appearance as shown in the diagram above.
MILLING BITS
Flat End Milling Bit
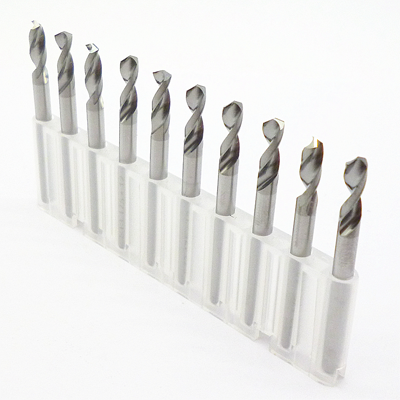
These ones are very flexible and can be used for many materials, even the hard ones. They are used to carve the material and take the most of it away without a second step. There are single or double fluted bits (actually, there are milling bits with up to eight flutes): the more you have, the harder the material can be. You wouldn’t use a single fluted one for metals.
The number of flutes increase with the hardness of the material. The FABtotum is able to work on any surface but it might be better to add another pass on the same route rather than going too strong.
Ball End Milling Bit
These are the ones needed to mill details or parts that require a nice and smooth finish. They can be fluted as well and the same idea as above applies.
The Ball End Mill, also known as Ball Nose milling bits, are the best option if the shape is not squared but has curves rounded angles.
They work perfectly with all surfaces but are likely to be chosen when a soft wood, balsa or foam is used. This is not a must but just an idea.
The presence of more flutes can add speed and precision, depending on how they spin: moving clockwise the flutes should take off more material while going backwards they would add a cleaner finish to the object.
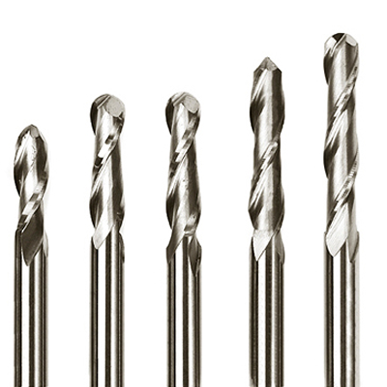
V Carve Milling Bit
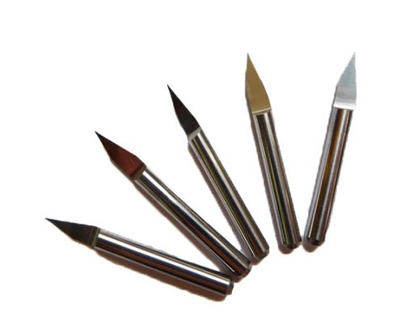
V carve flutes are used to engrave v-shaped paths and are usually associated with PCB engraving.They are differentiated by the angle of the tip. The bigger the angle the less probable is to break but it will be able to realize only bigger details, while smaller angles are used for fine details.